
The filter bags used in coal (biomass) boiler dust collectors are crucial components in the dust filtration system. Selecting the right filter bag material is essential for ensuring optimal filtration efficiency and reducing operational and maintenance costs.
When choosing filter bags, consider factors such as the temperature of the flue gas, the acidity or alkalinity of the emissions, and the characteristics of the dust. Typically, the exit flue gas temperature from boilers ranges from 100°C to 180°C and may have corrosive properties. Therefore, PPS filter bags (polyphenylene sulfide) are commonly recommended due to their excellent temperature resistance and corrosion resistance, providing superior filtration performance in harsh working conditions.
PPS filter bags are widely used for dust collection in oil-fired and coal-fired boilers as well as in waste incineration applications. Although the initial cost of PPS bags is relatively high, treating them with PTFE impregnation can extend their lifespan while maintaining compliance with emission standards, thus reducing overall maintenance costs.
Importance of Selecting the Right Filter Bag Material
The longevity of filter bags is significantly influenced by the choice of filter material. Historically, limited options and poor-quality materials resulted in short bag lifespans, leading to frequent replacements and increased operational costs. To avoid excessive pressure drops across the filter media, periodic cleaning of the filter bags is necessary. This cleaning process, typically using pulse jet technology, removes the majority of the dust layer while leaving a fine dust layer that aids in capturing smaller particles during the next filtration cycle.
Cost Considerations for Boiler Filter Bags
The cost of boiler filter bags varies significantly depending on the material chosen. Each type has its price point, so it’s important to select based on specific requirements. Our company specializes in manufacturing a range of boiler dust collector bags and related products. Below are some popular filter materials:
1. PTFE Fiberglass High-Temperature Filter Media:Known for its excellent acid and alkali resistance, this material is ideal for high-temperature and high-humidity environments. It is particularly effective in waste incineration, especially for handling high-viscosity dust and corrosive gases. This type of filter media has broad applications in industries including waste management, metallurgy, and cement production
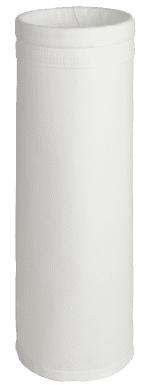
2. PPS Needle-Punched Felt Filter Bags:Operating at temperatures up to 160°C (short-term up to 190°C), these bags are highly resistant to acidic conditions. They perform exceptionally well in environments where sulfur compounds are present, making them suitable for coal-fired boilers and waste-to-energy plants.
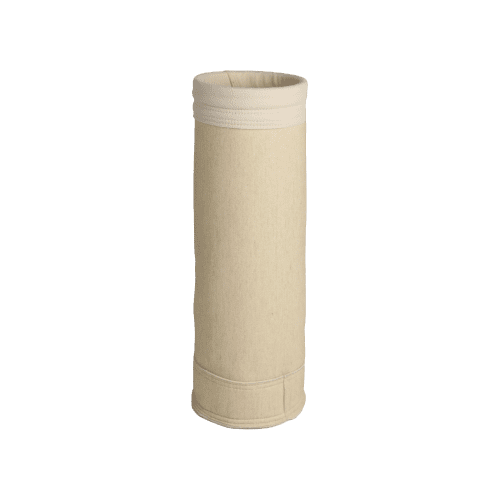
3. FMS Filter Bags:Featuring high-temperature resistance and durability, FMS bags are designed for various industrial applications. Their excellent filtration efficiency and low operating resistance make them a popular choice in sectors such as steel, chemical processing, and power generation.
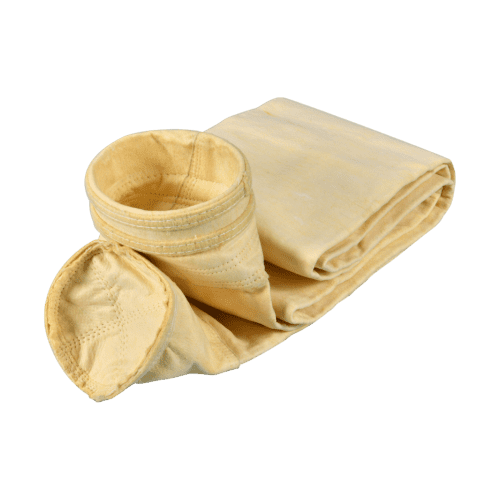
4. Fiberglass Needle-Punched Felt Filter Bags:4.This economical option provides high-performance filtration for high-temperature applications. It combines durability with cost-effectiveness, making it suitable for industries like metallurgy, cement, and chemical processing.
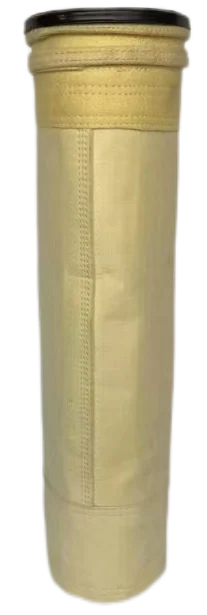
Ultimately, the choice of filter bag material should align with operational needs and budget considerations. Quality often correlates with cost—investing in higher-quality materials can lead to reduced long-term expenses and enhanced filtration performance.