Introduction to Dust Collector Bag Cages and Skeletons
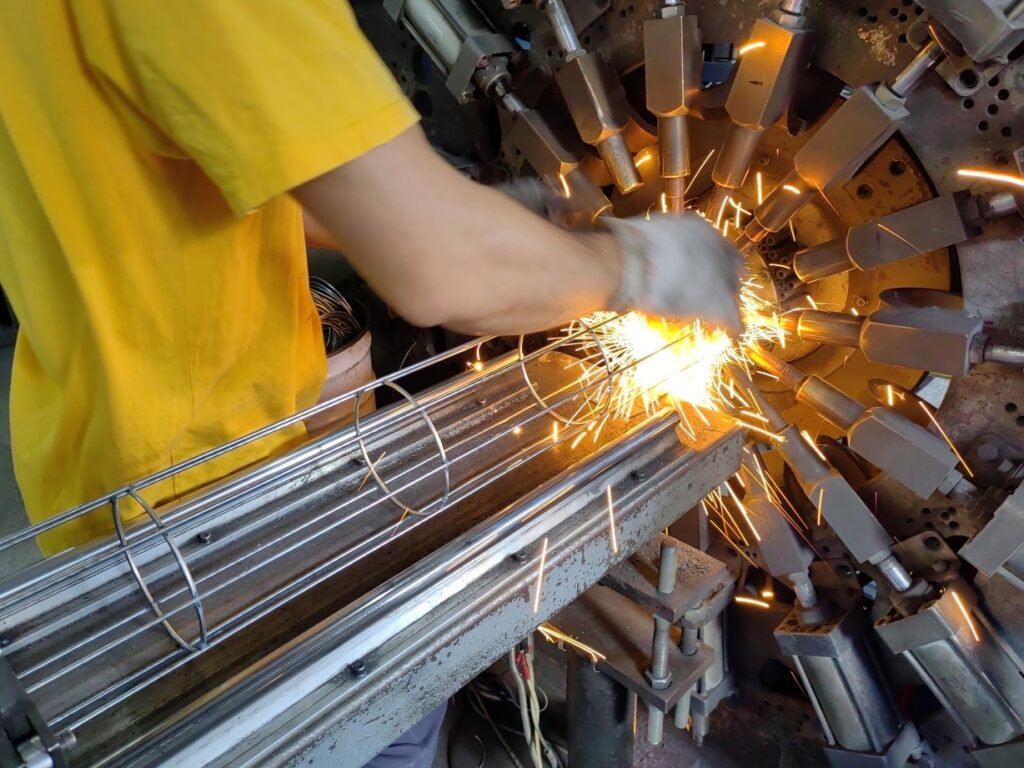
The dust collector skeleton, often referred to as the bag cage or dust bag cage, is a critical component of baghouse dust collectors. This structure supports the dust filter bags, ensuring they maintain their shape and perform efficiently during the filtration process. The quality of the dust collector skeleton directly impacts the performance and lifespan of the filter bags.
Key Production Technique for Dust Collector Bag Cages
One of the most common specifications for bag cages is the φ150×6000 model. This design features a circular structure with evenly distributed longitudinal bars and anti-bracing rings, providing the necessary strength and rigidity to prevent damage and deformation. The longitudinal rib diameter is typically ≥ φ4mm, with a reinforcing anti-bracing ring of φ4mm spaced 200mm apart. The top of the bag cage is equipped with an “η”-shaped cold stamping short pipe, ensuring the verticality of the bag cage and protecting the filter bag mouth during pulse jet cleaning.
The dust removal skeleton, or dust removal frame, is welded and formed using specialized equipment, characterized by firm welding and a smooth, straight appearance. It serves as the rib of the filter bag, and its quality significantly affects the bag’s working state and service life. The skeleton must be compatible with various rib configurations, including six, eight, ten, twelve, sixteen, eighteen, twenty, and twenty-four ribs.
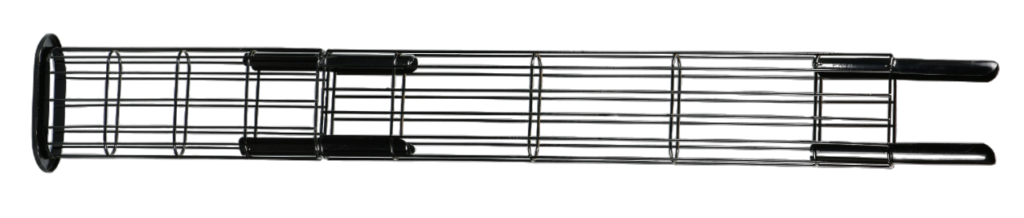
Essential Standards for High-Quality Dust Collector Bag Cages
- Strength and Rigidity: The dust collector bag cage requires evenly distributed support rings and longitudinal bars, with sufficient strength and rigidity to withstand gas pressure during filtration and ash cleaning. It must resist damage and deformation during transport and installation.
- Welding Quality: All solder joints of the filter bag cage must be firmly welded, with no desoldering allowed.
- Surface Smoothness: The surface of the filter bag cage in contact with the filter bag should be smooth and clean, without welding scars, unevenness, or burrs.
- Tension Spring Skeleton: The tension spring skeleton should have enough turns and elasticity, with uniform spacing after opening.
- Anti-Corrosion Treatment: The surface of the filter bag skeleton must undergo anti-corrosion treatment, such as electroplating, spraying, or painting, based on usage requirements. For high-temperature applications, the anti-corrosion treatment must meet the required temperature resistance.
- Verticality: The dust bag cage should maintain a verticality of ±1mm over a length of 6 meters.
- Sectional Design: The dust bag cage can be designed as a whole or in sections, with steel one-time forming tubes for lengths exceeding 3 meters.
- Surface Treatment: The dust bag cage is typically treated with galvanizing, plastic spraying, or silicone to enhance durability.
Matching Size and Durability for Optimal Dust Collector Performance
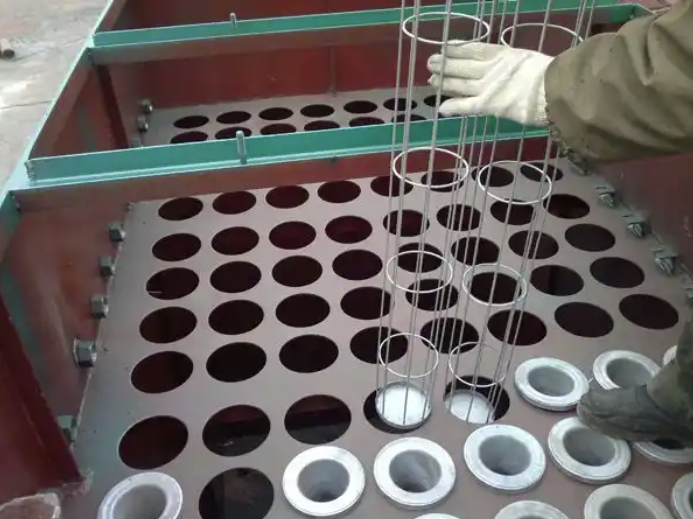
The gap between the dust bag and the skeleton is crucial for the baghouse’s service life. The dust removal skeleton acts as the rib of the dust collector, and proper sizing ensures that the bag is not damaged during pulse jet cleaning. Room temperature dust removal bags, such as polyester needle felt, generally have a weight of 450-550 grams per square meter, with a 10mm gap between the outer diameter of the skeleton and the inner diameter of the flower plate hole. High-temperature bags, like fluoromex needle felt or fiberglass needle felt, are thicker, weighing 650-950 grams per square meter, with a gap of at least 15mm.
Advantages of Pleated Dust Collector Bag Cages
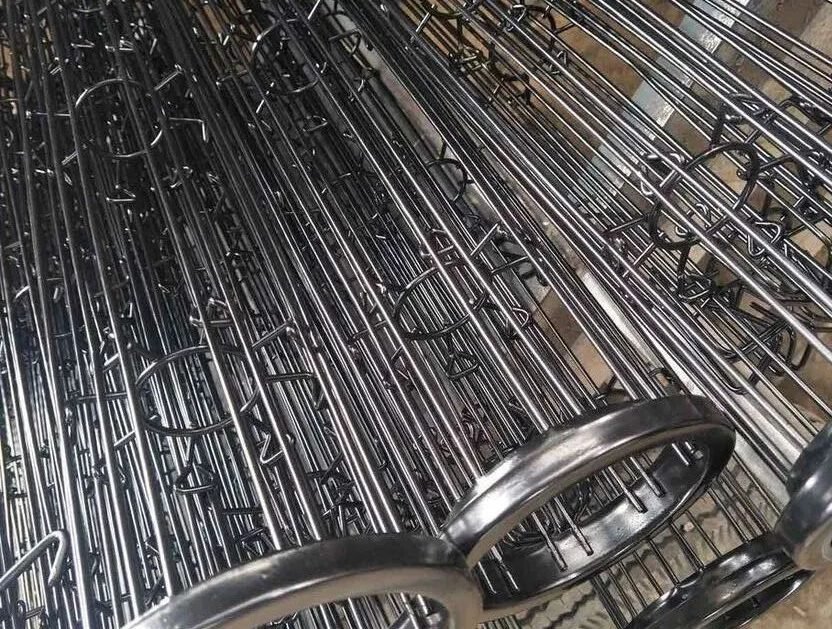
Pleated dust collector skeletons, which match pleated dust filter bags, offer several advantages:
- Increased Filtration Area: Compared to standard skeletons, pleated designs provide a larger filtration area, reducing costs.
- Various Specifications: Available in diameters of 120mm, 125mm, 150mm, and 155mm, with lengths ranging from 1 to 8 meters.
- Customization: Special models can be customized according to customer-provided drawings.
- Durable Surface Treatment: Common treatments include organic silicon, galvanizing, and plastic spraying, which extend service life, especially under high-temperature and corrosive conditions.
Pleated dust collector skeletons are made from high-quality carbon steel wire (φ6.5mm) drawn into φ3.7mm. They are welded using advanced one-time forming welding machines, ensuring a smooth, burr-free surface that prevents filter bag damage. The robust structure significantly extends the filter bag’s lifespan.
Conclusion: Enhancing Dust Collection Efficiency with Quality Bag Cages
In conclusion, the dust collector skeleton, or bag cage, is a vital component of baghouse dust collectors. Its design, material quality, and surface treatment directly influence the performance and longevity of the dust collection system. Proper sizing and high-quality construction are essential for ensuring optimal filtration and maintaining the integrity of the filter bags during operation.
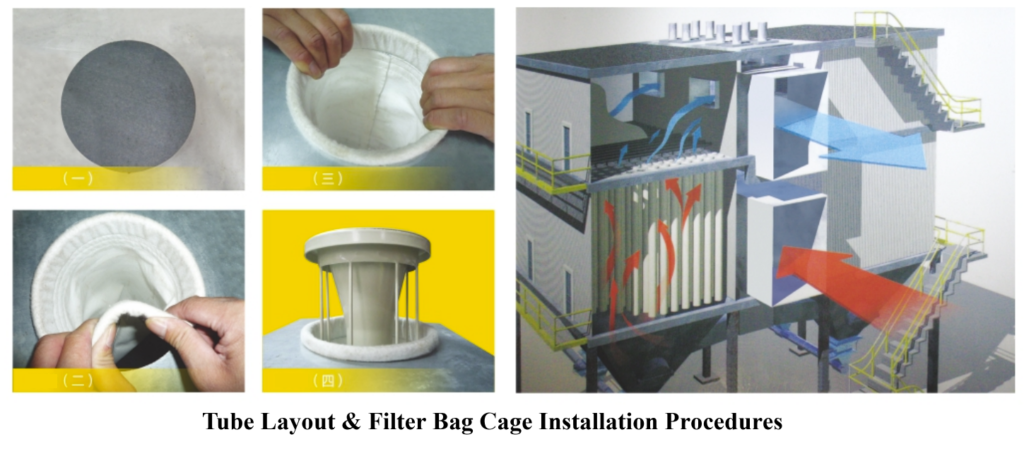